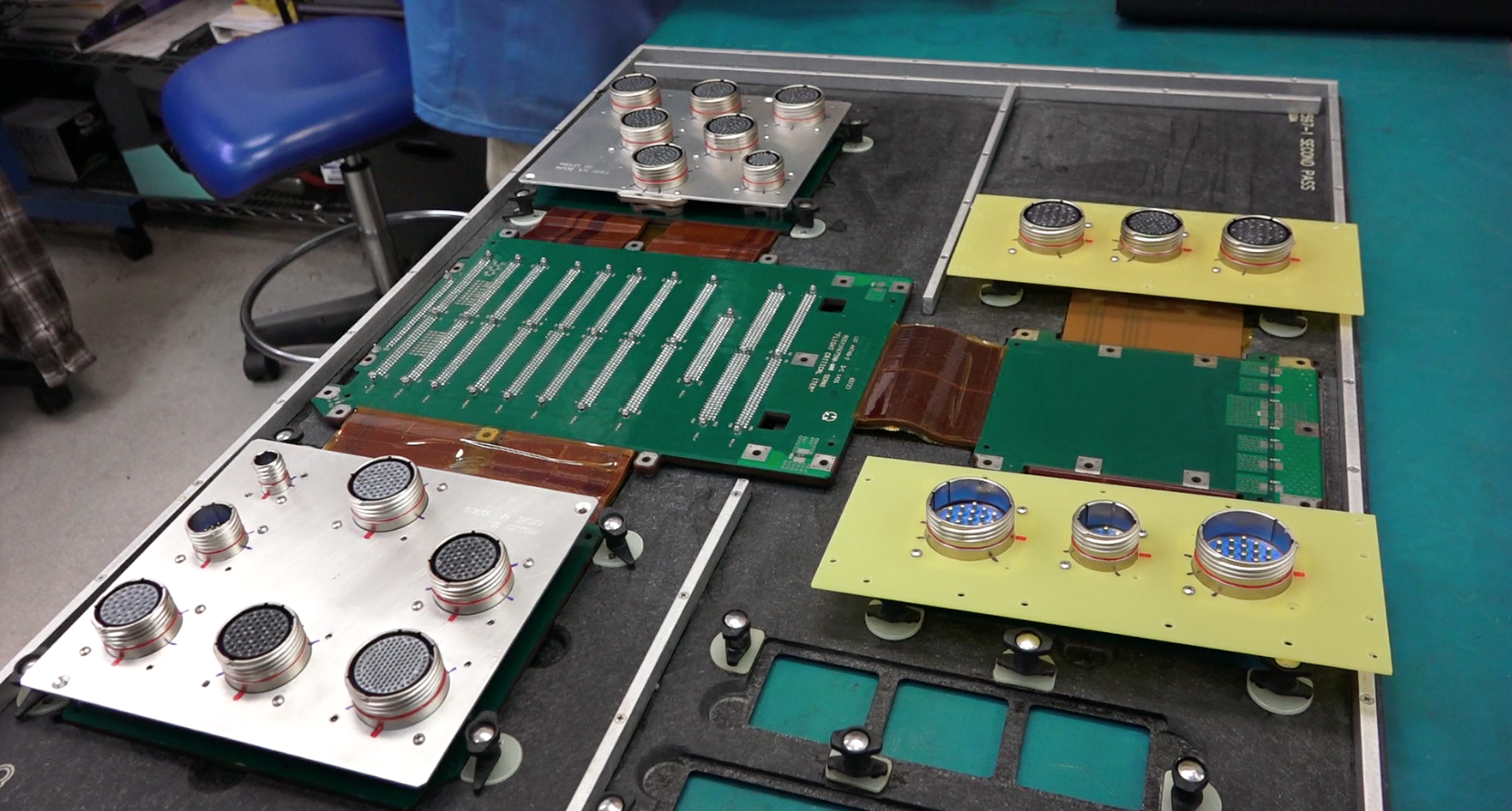

Pioneer Circuits, Inc
Advanced Interconnection Solutions
Flex & Rigid-Flex PWB Manufacturing
Pioneer Circuits is the worldwide leader in fabricating high technology flex and rigid-flex designs. Our Specific capabilities include:
-
High Layer Count – misregistration is typically a major yield driver in flex/rigid-flex manufacturing. Pioneer overcomes this issue with a unique tooling system that allows us to fabricate products in excess of 30 layers.
-
Oversize – profile dimensions as large as 22” X 34” are routine at Pioneer with some panels as large as 60” in length.
-
Bookbinders – are often the best or only way to achieve a tight bend radius with multiple flex layers. Experience, special tooling and equipment modifications allow us to fabricate bookbinder designs without substantial additional cost or yield loss.By staggering the length of each flexible layer, a bookbinder construction eliminates the buckling and greatly reduces the compression/tension forces that are introduced when a PWB with multiple flex layers is bent into its installed configuration. The result is a much more flexible and durable end product. A study by the University of Arkansas for NASA/JPL confirmed the dramatic in crease in reliability achieved with a bookbinder construction.In most cases, the customer generated artwork received by Pioneer for a bookbinder design does not contain staggered length flex layers. Pioneer’s pre-production engineering department will then calculate the appropriate staggers based on the installed configuration of finished product and apply a corresponding ‘stretch’ to specific section(s) of the flexible layers.
-
Microvias (HDI)/Blind Via/Buried Via – virtually all of today’s advanced rigid PWB manufacturing technologies can be used in rigid-flex designs. Pioneer has extensive experience fabricating rigid-flex PWB’s with features such as laser drilled microvias, sequential laminations, filled vias, via-in-pad and other advanced construction technologies. (Pioneer to supply new photos of microvia x-sections to illustrate)
-
Controlled Impedance – although a very common requirement in today’s PWB’s, rigid-flex designs present some unique challenges to achieving impedance matching requirements. Pioneer’s engineers are well versed in the theoretical and practical applications of controlled impedance in rigid-flex designs and can assist with impedance modeling, materials selection, test data, etc.
-
Constantan – may be used in place of copper to form conductors when heat load is a major consideration. Typical applications for this type of thermal management are focal plane arrays in infrared (IR) imaging equipment. Pioneer’s extensive experience with manufacturing constantan flex circuitry has led to several unique/advanced capabilities including adhesiveless constantan laminates and controlled resistance via copper microplating.
-
Thin core – 1 and 2mil core flexible polyimide film laminates can be replace the typical polyimide/glass or epoxy/glass rigid cores in rigid and rigid-flex constructions to minimize overall thickness
-
Silver Ink Shielding – Dupont CB028 is a flexible silver loaded polymer ‘ink’ specifically created for EMI/RFI shielding on flex circuitry. Substantial gains in flexibility can be achieved in many cases by replacing the copper shield layers with silver ink. Standard silk screening techniques are typically used to apply the ink. The average thickness of the silver ink layer is approximately 1 mil.
-
Special projects
-